Our Process | Boll & Branch
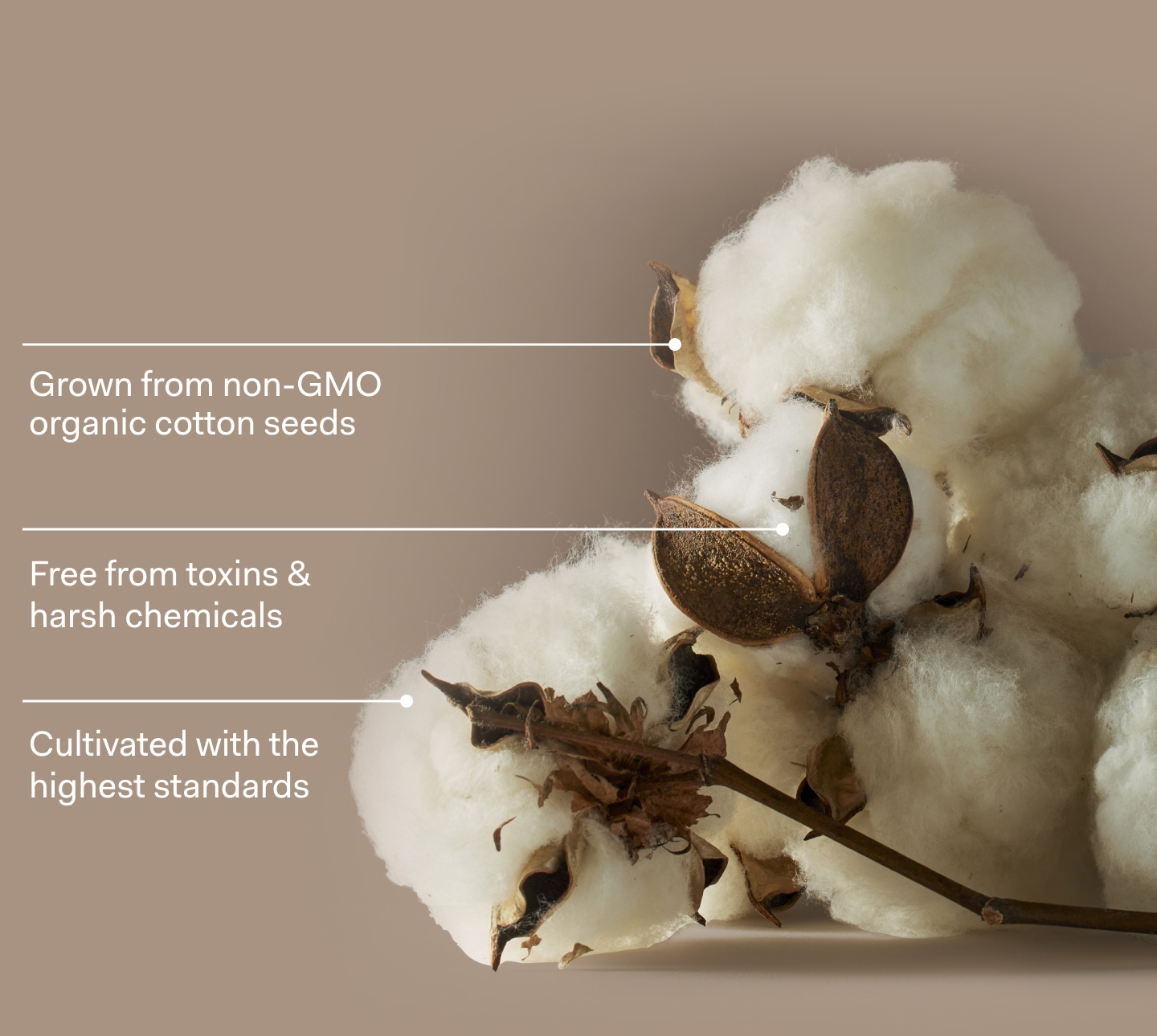
Choosing Different From The Seed
While conventional cotton relies on synthetic chemicals including pesticides, herbicides, and fertilizers, and is usually grown from genetically modified (GMO) seeds, organic cotton is cultivated using environmentally conscious agricultural methods and adheres to stringent ethical standards, ensuring better conditions for farmers and ecosystems.
Learn more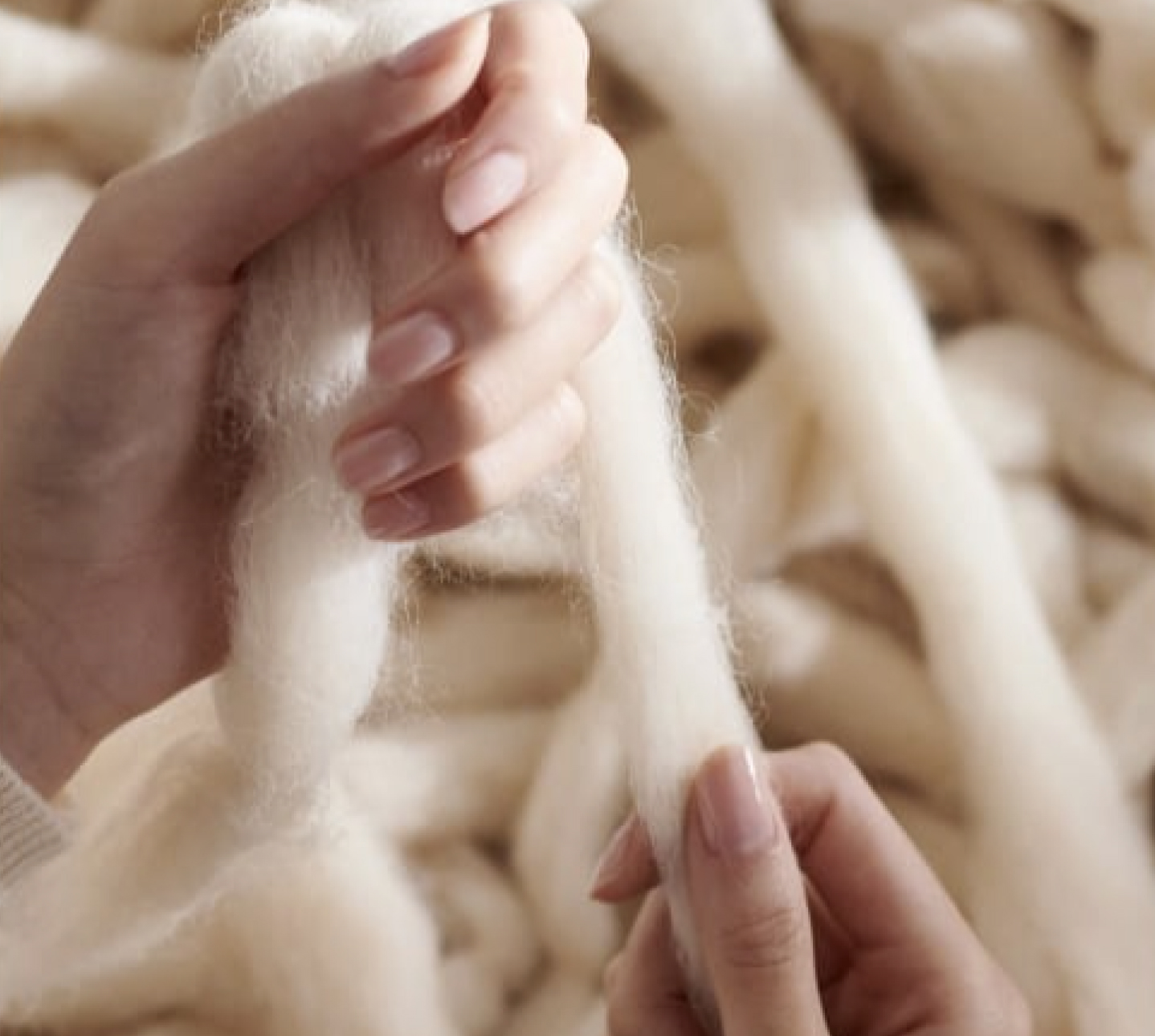
Setting A Higher Standard At Every Step
At this stage, impurities are removed from the cotton (ginning) and the spinner selects the fiber by staple length (we choose the longest staple length possible) before it’s twisted into threads (spun). We take additional steps to reduce waste: at this step, the cotton seeds are sold and repurposed into cottonseed oil (to cook with), with proceeds going to the farmers.
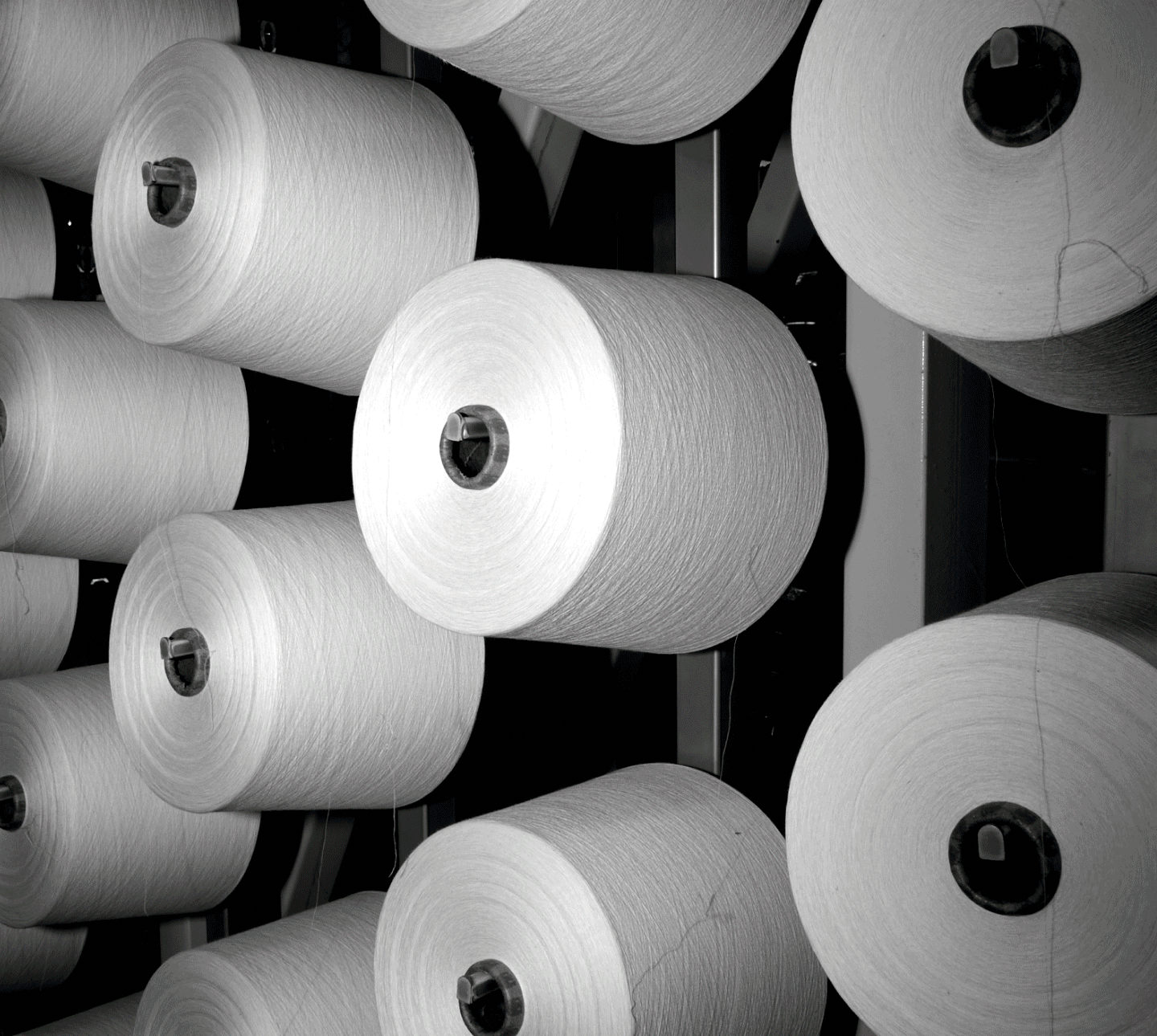
Cultivating The Highest Quality Threads
Fabric making always begins by setting up the warp, an intensive process of individually threading the yarn through thousands of eye-holes. To strengthen our threads, we use a natural potato and wheat based recipe—not acrylics, as conventional cotton often uses—which wash away after the fabric is woven. The horizontal yarn, called the weft, is then shot across the warp in a pattern that determines the experience of the fabric. All of this is done in environments that are audited for both organic standards, and safe working conditions.
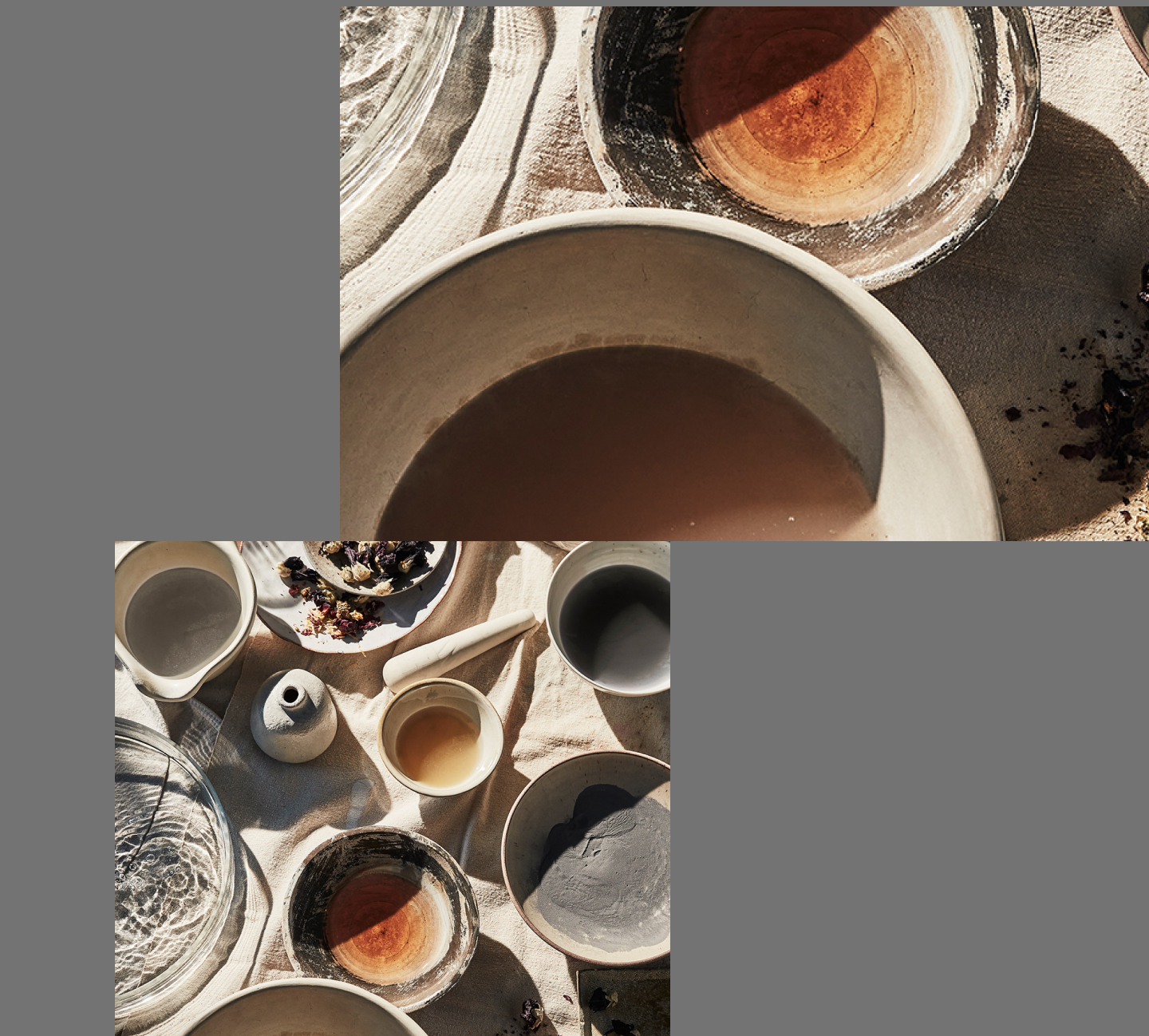
Creating The Softest, Most Serene Palette
Using our proprietary color palette, we dye the fabric, ensuring the process is free from harmful chemicals and toxins. This guarantees that our sheets are not just pleasing to the eye, but also safe for your skin and the environment. Additionally, the use of synthetic inputs is forbidden, including antimicrobial, coating, filling, stiffening, lustring, matting, and weighting processes that can be used in conventional cotton manufacturing. Finishing methods like sand blasting, which are considered harmful to workers, are also prohibited.
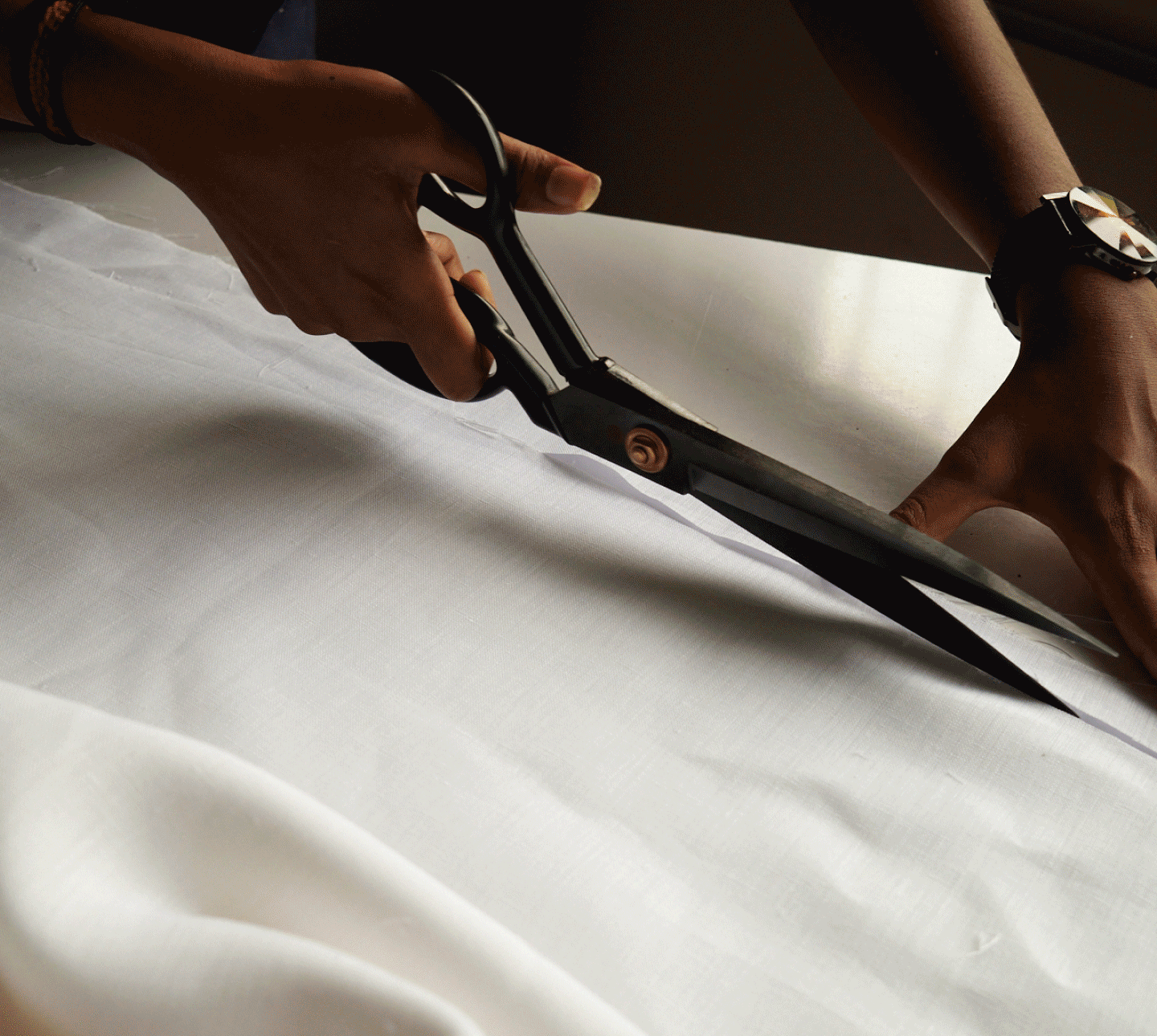
Ensuring Every Detail Is Considered
While techniques for making each of our fabrics are specialized for the experience, there are approximately 50+ operations from cutting to final product for our sheet sets. We developed a unique process to ensure quality control at each step. A third-party auditor is stationed at each of our factories daily. Unlike most in the industry who have them come in and out of the process, our quality team stays full time at each of our sheeting facilities to oversee the process, and partners with our mills on quality and production efficiency.
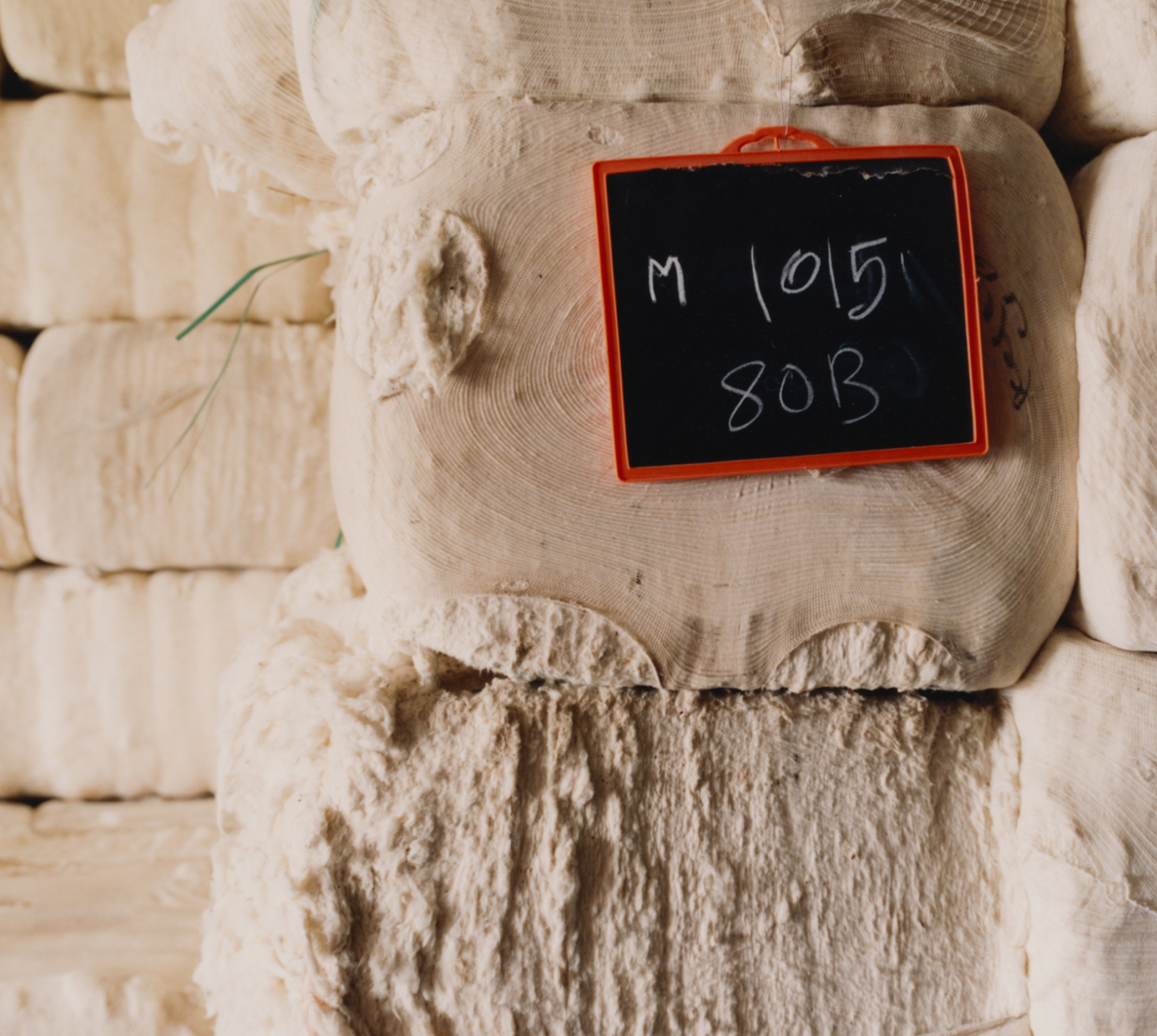
How We Hold Our Partners To Higher Standards
Boll & Branch requires all partners to be certified to top social certification standards (82% of our partners have Fair Trade USA, SA8000, or WRAP). Any supplier who does not have one of these certifications, must pass a comprehensive Boll & Branch Ethical & Social audit to ensure they conduct business operations in line with our company values of humanity, responsibility, and intention.
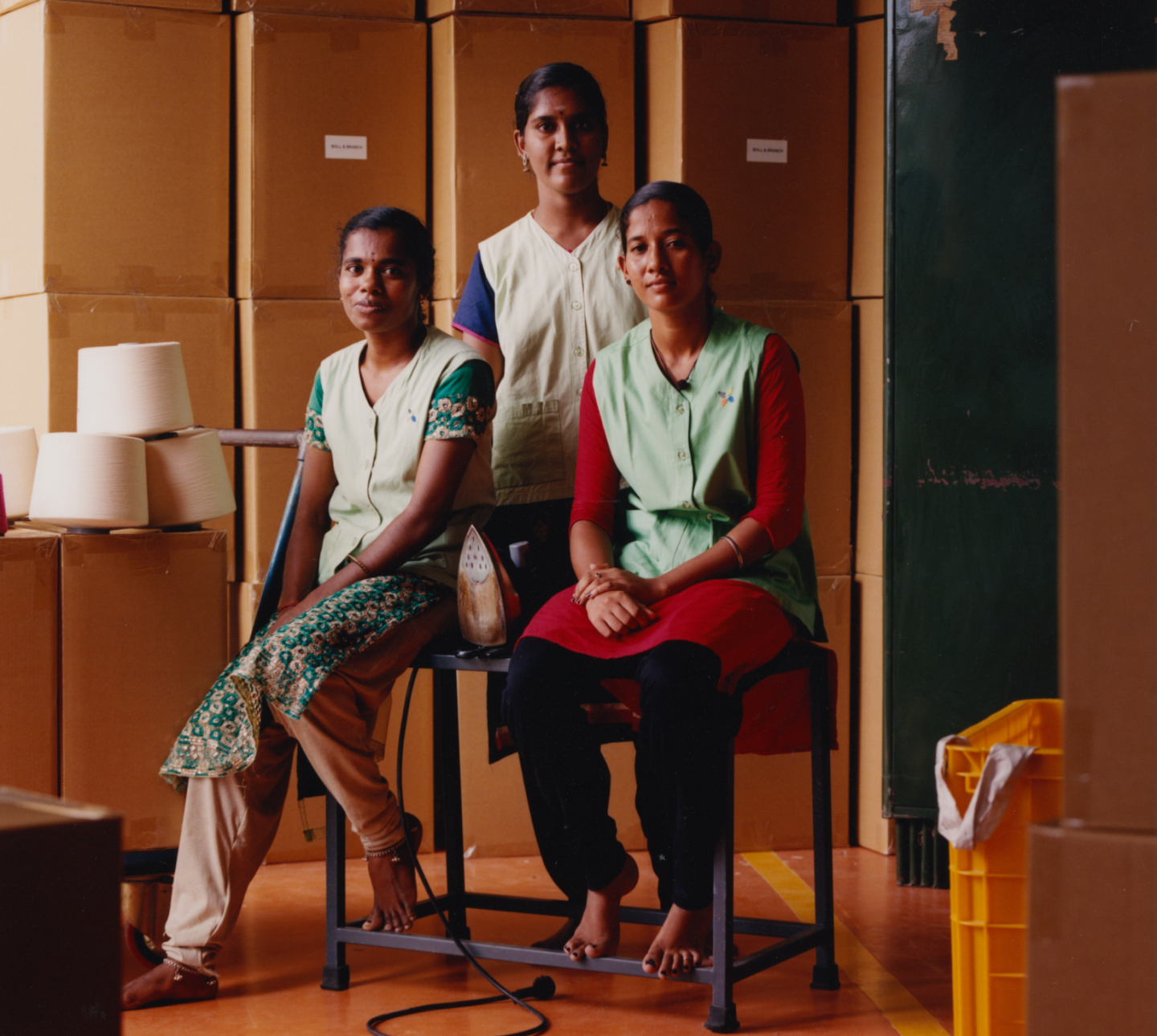
An Unwavering Commitment To Change The Status Quo
The above mentioned certifications and auditing bodies ensure our products are produced according to rigorous standards and challenge practices that are a blight on the bedding industry and manufacturing at large. We only work with partners that prioritize: no child labor, no discrimination, fair wages, a safe and healthy workplace, increased awareness of workers rights, and a culture for continuous improvement.